Since this journal post, we have stopped selling letterpress prints. We continue to print packaging for our range of industrial lighting products using letterpress and personalise Moleskine and Lecuhtturm1917 notebooks using mechanical typesetting and letterpress.
Original post: While the weather outside is close to freezing, the print team at the Old Trouser Factory have had a sweat on! We recently began experimenting with posters - printing some of the great artwork from our range of personalised greeting cards on letterpress posters. Ever since our collaboration with Print Club London started last autumn, we've had in mind the creation of letterpress posters on our Heidelberg 13 x 18 machine. Our print run of Walter White or Heisenberg Christmas cards gave us confidence we could print letterpress posters. Heisenberg was a single colour of dark ink with a large print area. It was a good test of the accuracy of our plate mounting base and it passed with flying colours - the image was extremely clean and even.
Having run a few additional tests, we were reasonably confident that we could produce a single colour A3 letterpress poster. We decided to try a run of posters featuring the 'Love 24 Seven 365' design by Alice Stallard. After a few torn sheets, and adjustments to the ink flow and inking roller height, the test was a success. We produced a clean, fine and detailed result which seemed to confirm we were good for a full production run of letterpress posters.
Over the next couple of days the large Heidelberg was in use for other print requirements. At the end of a run we found ourselves with black ink on the machine - perfect for producing letterpress posters of Susie Wright's 'Bear' design. We imagined it would be a simple printing process, but when the design was scaled up from greeting card to poster size it contained a much greater area of print than we first thought. We struggled to produce an even print because of variable surface accuracy of our plate mounting base.
We improvised and added 80gsm paper under the platen top sheet and various weights of tissue paper between the plate base and type bed. We were pleased when we managed to produce a clean run of the design because the letterpress posters were required for a Print Club London event! With some cutting down, the addition of embossed design elements and some limited edition numbering, the letterpress posters were ready for their London trip.
Despite our successful improvisation, we decided that a more accurate base was required for big areas of print. We ordered a custom large plate base of the same design as the smaller bases we use to print greeting cards. The base arrives fresh from the mill in a few weeks time.
With no time to waste, we decided to move on to another letterpress poster run, the 'Love 24 Seven 365' design, but this time in its vivid pink livery. We assumed this run would be a piece of cake compared to the Bear: we'd matched the colour before, the plate was proven in a previous test and the area of printing was much less than Heisenberg and the Bear. We had no idea how wrong we were. With minimal ink coverage the print began to 'repeat' leading to patchy results. The problem was caused by the circumference of the inking rollers being less than the length of the sheet, even at its shortest dimension. Coverage could be achieved with lots of ink but this made the image darker - almost red - rather than the desired pink tone.


In order to rectify the problem we attempted several fixes. We first mixed the ink to a paler tone, but this did little to help with transparency even with a high ink flow. We then replaced the roller trucks hoping that a smoother ink-up on the plate would work. This change did help a little, but not enough. The final idea was to introduce the pair of steel rider rollers that sit on top of the inkers to act as a reservoir.

Again, this change did improve the print but not to the standard we expect of the print products we sell. Our conclusion was that we were not going to be able to consistently produce letterpress posters on our current machines, or not ones we would sell to our discerning customers!
Our bold solution is to add to our family of original Heidelberg presses. Negotiations are underway to buy a larger Heidelberg 18 x 23 cylinder press. As the name suggests, this larger press can print up to 18 x 23 inches or 457mm x 584mm - almost A2 size. With luck, the new press will be with us and producing fantastic letterpress posters in the next month. The new press looks like this.
What a beast! We're very excited and will post again with photos when our new vintage Heidelberg arrives.
Original post: While the weather outside is close to freezing, the print team at the Old Trouser Factory have had a sweat on! We recently began experimenting with posters - printing some of the great artwork from our range of personalised greeting cards on letterpress posters. Ever since our collaboration with Print Club London started last autumn, we've had in mind the creation of letterpress posters on our Heidelberg 13 x 18 machine. Our print run of Walter White or Heisenberg Christmas cards gave us confidence we could print letterpress posters. Heisenberg was a single colour of dark ink with a large print area. It was a good test of the accuracy of our plate mounting base and it passed with flying colours - the image was extremely clean and even.

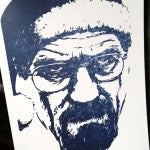





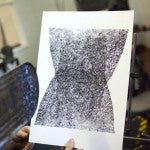

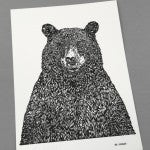







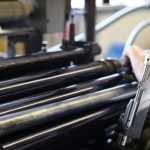
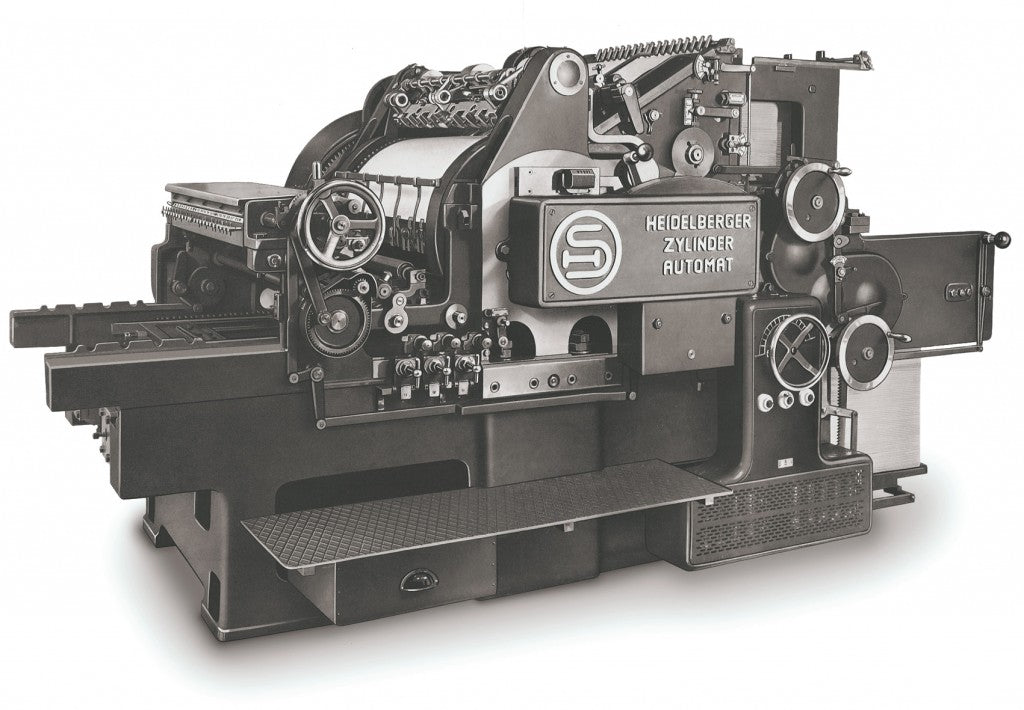
Leave a comment
This site is protected by hCaptcha and the hCaptcha Privacy Policy and Terms of Service apply.